What is asset performance management (APM)?
Asset performance management (APM) refers to industry practices, strategies, and software tools to optimize the performance, reliability, and lifespan of their physical assets, such as machinery, equipment, infrastructure, or facilities.
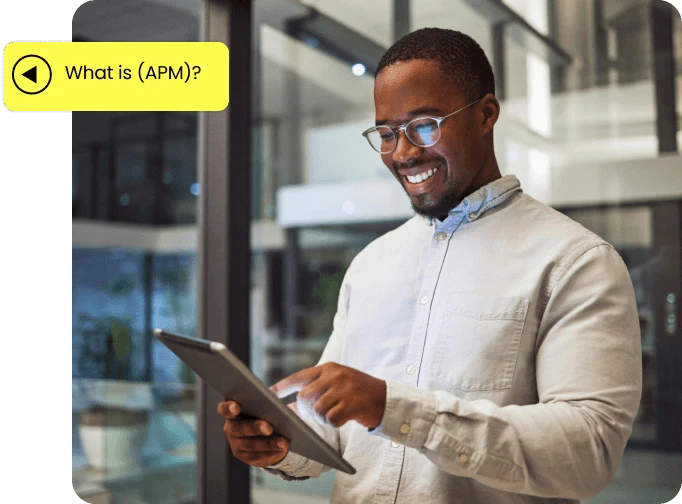
Table of contents
APM involves monitoring, analyzing, and managing various aspects of asset performance, including maintenance, operations, safety, and efficiency, to maximize productivity, minimize downtime, reduce operational costs, and extend the useful life of assets. This is typically achieved through advanced analytics, predictive maintenance techniques, condition monitoring, and data-driven decision-making. Asset performance management (APM) encompasses several key components and processes to improve the performance and reliability of assets within an organization.
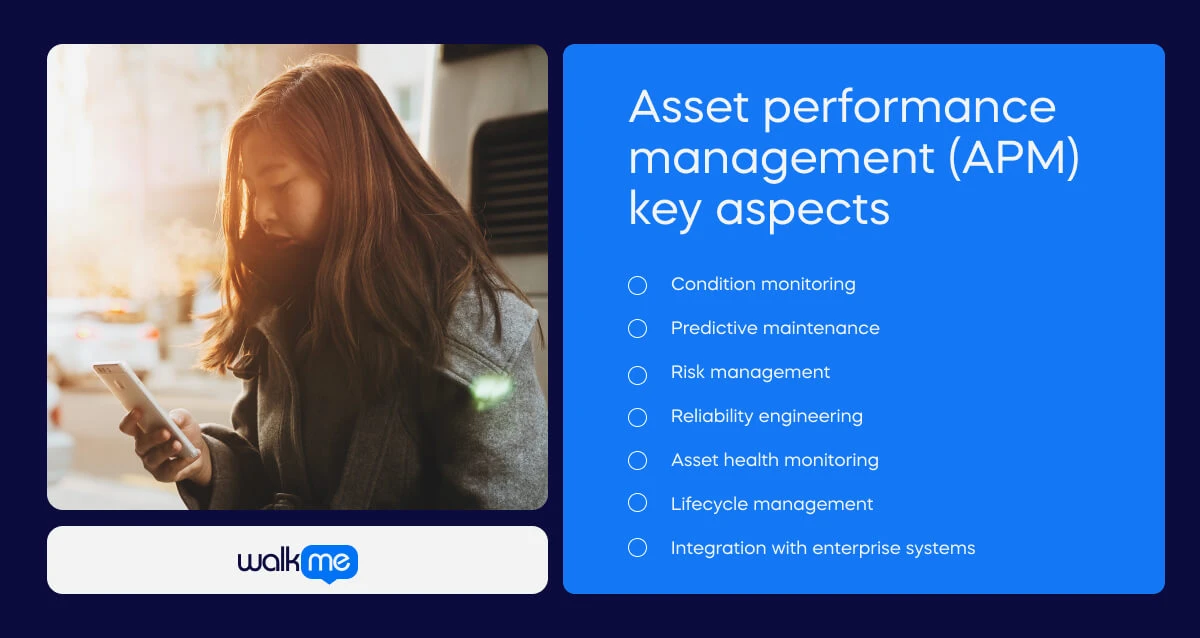
Here are some of the key aspects in more detail:
Condition monitoring
APM involves continuously monitoring the condition of assets in real-time or at regular intervals to detect any abnormalities, deviations from expected performance, or signs of potential failure. This can include collecting data such as temperature, vibration, pressure, fluid levels, and other relevant parameters using sensors and monitoring systems.
Predictive maintenance
A key aspect of APM is the implementation of predictive maintenance techniques, which use data analytics, machine learning, and statistical modeling to predict when equipment will likely fail or require maintenance. Organizations can schedule maintenance activities proactively by analyzing historical performance data and identifying patterns or trends, minimizing unplanned downtime and reducing maintenance costs.
Risk management
The practice includes assessing and managing risks associated with asset performance, including identifying potential failure modes, evaluate the likelihood and consequences of failures, and implementing strategies to mitigate risks. This may involve prioritizing maintenance tasks, implementing redundancy or backup systems, and establishing contingency plans.
Reliability engineering
APM incorporates principles of reliability engineering to design, operate, and maintain assets to maximize reliability and availability. This includes optimizing asset designs, selecting appropriate materials and components, establishing maintenance strategies, and continuously improving asset performance through feedback and iteration.
Asset health monitoring
These systems provide insights into the overall health and condition of assets, allowing organizations to track performance metrics, assess asset reliability, and identify opportunities for optimization. This may involve generating key performance indicators (KPIs), dashboards, and reports to monitor asset health and performance over time.
Lifecycle management
APM considers the entire lifecycle of assets, from design and procurement to operation and decommissioning. By taking a lifecycle approach, organizations can make informed decisions about asset investments, upgrades, and replacements, optimizing asset performance and total cost of ownership over time.
Integration with enterprise systems
The solutions are often integrated with other enterprise systems, such as Enterprise Asset Management (EAM), Computerized Maintenance Management Systems (CMMS), and Supervisory Control and Data Acquisition (SCADA) systems, to streamline data management, workflow automation and decision-making processes.
Use cases for asset performance management (APM)
Asset performance management (APM) in business
Asset performance management (APM) finds practical applications across various industries and contexts, enabling organizations to optimize the performance, reliability, and longevity of their assets. Here are some scenarios illustrating how APM is actively utilized across different features and functionalities:
Manufacturing industry
Predictive maintenance: In manufacturing, APM systems can predict equipment failures before they occur by analyzing real-time sensor data and historical maintenance records. This allows manufacturers to schedule maintenance during planned downtime, minimizing disruptions to production.
Asset health monitoring: APM solutions continuously monitor the health and performance of manufacturing equipment, identifying potential issues such as excessive vibration, temperature deviations, or lubrication problems. This helps manufacturers proactively address issues before they escalate into costly failures.
Reliability engineering: Manufacturers use APM principles to optimize the reliability and availability of critical assets, such as production machinery and assembly lines. Manufacturers can improve overall equipment effectiveness (OEE) and reduce downtime by implementing reliability-centered maintenance strategies and optimizing asset designs.
Oil and gas industry
Condition monitoring: APM systems monitor the condition of oil and gas assets, such as pumps, compressors, and pipelines, to detect early signs of wear, corrosion, or mechanical failures. This allows operators to take corrective actions, such as adjusting operating parameters or scheduling maintenance, to prevent costly downtime and ensure safety.
Risk management: With these solutions, oil and gas companies can assess and manage risks associated with asset performance, such as equipment failures, safety incidents, and environmental hazards. By analyzing risk factors and implementing mitigation measures, operators can minimize the likelihood and impact of adverse events.
Asset integrity management: These systems support asset integrity management programs by providing insights into the integrity, reliability, and compliance of critical infrastructure assets. This includes conducting risk-based inspections, monitoring corrosion rates, and prioritizing maintenance activities based on asset criticality and regulatory requirements.
Utilities sector
Grid asset management: APM solutions are used in the utilities sector to manage the performance and reliability of electrical transmission and distribution assets, such as substations, transformers, and power lines. Utilities can optimize maintenance schedules, improve grid reliability, and minimize outage durations by monitoring asset health and predicting failures.
Condition-based maintenance: Utilities leverage APM systems to implement condition-based maintenance strategies, where maintenance activities are triggered based on the actual condition of assets rather than fixed time intervals. This approach reduces unnecessary maintenance costs and extends the useful life of assets while ensuring reliability and safety.
Remote monitoring and diagnostics: APM platforms enable utilities to monitor and diagnose asset performance issues remotely, particularly for geographically dispersed assets or remote substations. By collecting data from sensors and remote monitoring devices, operators can identify problems early and dispatch maintenance crews efficiently.
Success stories with asset performance management (APM)
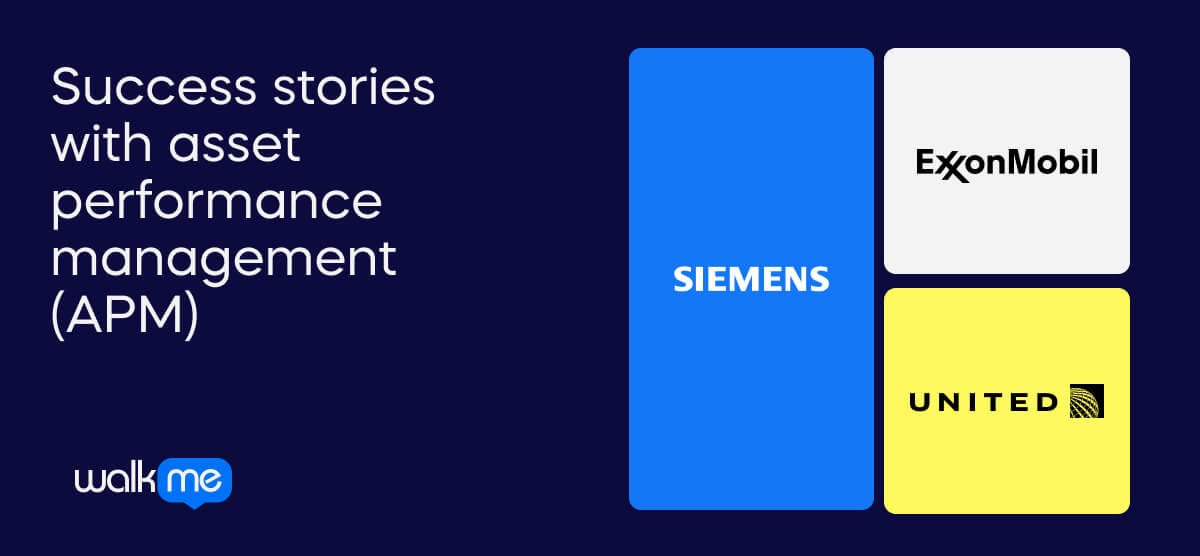
Here are some examples of well-known companies that have successfully implemented asset performance management (APM) strategies:
ExxonMobil
ExxonMobil, one of the largest publicly traded international oil and gas companies, has integrated APM into its operations to optimize the performance and reliability of its refining, petrochemical, and upstream assets. Through APM, ExxonMobil has improved asset reliability, reduced maintenance costs, and enhanced safety and environmental performance. They can proactively address equipment failures and optimize maintenance schedules by leveraging data analytics and predictive maintenance techniques.
Siemens
Siemens, a global technology conglomerate, offers APM solutions as part of its Digital Industries portfolio to help customers in various industries optimize asset performance and maintenance. Siemens’ APM solutions utilize advanced analytics, IoT connectivity, and machine learning algorithms to monitor equipment health, predict failures, and optimize maintenance activities. Customers benefit from improved asset reliability, reduced downtime, and increased operational efficiency across their industrial operations.
United Airlines
United Airlines, a major American airline, has adopted APM to optimize the performance and reliability of its aircraft fleet and ground support equipment. Through APM, United Airlines can monitor the health of critical aircraft components, predict maintenance needs, and optimize maintenance schedules to ensure fleet reliability and safety. APM helps United Airlines minimize disruptions, improve on-time performance, and enhance the overall passenger experience.
Examples of asset performance management (APM)
How businesses find success with asset performance management (APM)
Here are three examples of organizations successfully leveraging asset performance management (APM) for their digital adoption strategy:
Tesla: Predictive maintenance
Tesla, the electric vehicle and clean energy company, utilizes APM for predictive maintenance of its manufacturing equipment and vehicle fleet. By analyzing real-time data from sensors embedded in its vehicles and manufacturing equipment, Tesla can predict potential failures and schedule proactive maintenance before issues escalate. Predictive maintenance helps minimize downtime on the assembly line, ensuring consistent production output. Additionally, proactive maintenance of vehicles leads to enhanced reliability and customer satisfaction.
Amazon Web Services (AWS): Asset health monitoring
AWS, the cloud computing division of Amazon, employs APM to monitor the health and performance of its data centers and infrastructure. APM systems continuously collect and analyze data on server performance, network traffic, and hardware health to identify potential issues and optimize resource allocation. Asset health monitoring allows AWS to proactively address performance bottlenecks and hardware failures, ensuring high availability and reliability for customers’ applications and data.
Delta Air Lines: Risk management
Delta Air Lines, a major airline, leverages APM for risk management of its aircraft fleet and maintenance operations. APM systems analyze data from aircraft sensors, maintenance records, and flight operations to assess the risk of component failures, operational disruptions, and safety incidents. By proactively identifying and mitigating risks, Delta can enhance safety standards, minimize flight delays and cancellations, and optimize maintenance schedules, resulting in a smoother travel experience for passengers and improved profitability for the airline.
Asset performance management (APM) vs software performance management (SPM)
Asset performance management (APM) and software performance management (SPM) are two distinct concepts, although they share some similarities in terms of their focus on optimizing performance. Let’s compare the two:
Asset performance management (APM)
Asset performance management (APM) is a discipline focused on maximizing the performance and reliability of physical assets within industrial settings, such as machinery, equipment, or infrastructure. APM involves using technology and data analytics to monitor asset health, predict failures, and optimize maintenance strategies to ensure that assets operate at peak efficiency and availability.
Key components of APM include:
Condition monitoring APM systems use sensors, IoT devices, and other monitoring technologies to continuously collect data on asset conditions, performance, and operating parameters in real-time.
Predictive maintenance APM leverages predictive analytics and machine learning algorithms to analyze asset data and predict when maintenance is required before failures occur. This allows organizations to schedule maintenance proactively, minimize downtime, and extend asset lifespan.
Asset health monitoring APM solutions provide insights into the overall health and reliability of assets by aggregating and analyzing data on equipment performance, maintenance history, and operational metrics.
Asset reliability management APM improves asset reliability by identifying and mitigating potential failure modes, optimizing maintenance strategies, and implementing reliability-centered maintenance (RCM) practices.
Performance optimization APM helps organizations optimize asset performance by identifying opportunities for efficiency improvements, reducing energy consumption, and maximizing asset utilization.
Software performance management (SPM)
Software performance management (SPM) is a discipline focused on monitoring, analyzing, and optimizing the performance of software applications and IT systems. SPM involves using tools and techniques to measure various aspects of software performance, such as response times, throughput, resource utilization, and reliability.
Key components of SPM include:
Application performance monitoring (APM) SPM solutions provide real-time visibility into the performance of software applications by monitoring metrics such as response times, transaction throughput, error rates, and resource utilization.
Infrastructure monitoring SPM tools monitor the underlying infrastructure (e.g., servers, databases, networks) to identify performance bottlenecks, resource contention issues, and other factors impacting software performance.
End-user experience monitoring SPM solutions track user interactions with software applications to assess the quality of the end-user experience, identify usability issues, and troubleshoot performance problems.
Performance diagnostics and troubleshooting SPM tools provide diagnostics and troubleshooting capabilities to help identify the root causes of performance issues, optimize software configurations, and improve system performance.
Capacity planning and optimization SPM involves capacity planning activities to ensure software applications have sufficient resources to meet performance requirements under varying workloads. This includes forecasting resource demands, scaling infrastructure as needed, and optimizing resource allocation.
Asset performance management (APM) focuses on optimizing the performance and reliability of physical assets, while Software Performance Management (SPM) focuses on maximizing the performance of software applications and IT systems. Both disciplines involve monitoring, analyzing, and optimizing performance within different contexts and domains.
Advantages of asset performance management (APM)
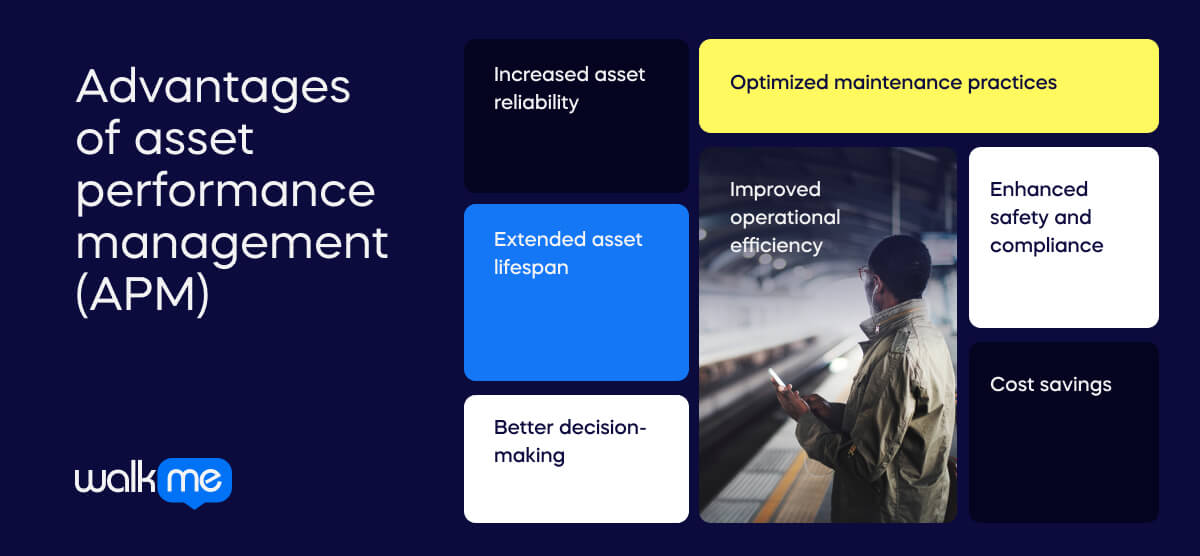
Asset performance management (APM) offers several advantages for organizations looking to optimize the performance and reliability of their assets. Some key advantages include:
Increased asset reliability
APM helps organizations improve the reliability of their assets by proactively monitoring equipment health, detecting potential issues early, and implementing preventive maintenance strategies. This reduces downtime, fewer unplanned outages, and enhanced operational reliability.
Optimized maintenance practices
APM enables organizations to move from reactive or scheduled maintenance to more proactive and predictive maintenance approaches. Organizations can identify patterns, predict failures, and optimize maintenance schedules by analyzing data from sensors, historical maintenance records, and other sources, resulting in reduced maintenance costs and improved asset availability.
Extended asset lifespan
By implementing effective maintenance strategies and addressing issues before they escalate, APM helps organizations extend the useful life of their assets. This maximizes the return on investment (ROI) for capital-intensive assets and defers the need for costly replacements or upgrades.
Improved operational efficiency
APM gives organizations insights into asset performance, utilization, and efficiency, allowing them to optimize asset operations and resource allocation. Organizations can improve overall operational efficiency and productivity by identifying inefficiencies, optimizing workflows, and minimizing downtime. For example, APM and asset analytics allow facilities in the oil and gas industries to reduce downtime by proactively recognizing and preventing failures while reducing unnecessary routine inspection and maintenance, according to IDC.
Enhanced safety and compliance
APM helps organizations maintain regulatory compliance and mitigate safety risks by monitoring asset health, identifying potential hazards, and implementing appropriate control measures. Organizations can minimize the risk of accidents, incidents, and regulatory penalties by ensuring that assets are operating within safe parameters and meeting regulatory requirements.
Better decision-making
APM provides organizations with actionable insights and data-driven decision support, enabling them to make informed decisions about asset investments, maintenance priorities, and operational strategies. By leveraging real-time data and predictive analytics, organizations can optimize asset performance, reduce operational risks, and maximize business value.
Cost savings
Ultimately, APM helps organizations reduce operational costs, optimize capital investments, and improve overall financial performance. By minimizing unplanned downtime, reducing maintenance expenses, and extending asset lifespans, organizations can achieve significant cost savings over time, leading to improved profitability and competitiveness. For example, Deloitte reports that an APM application in a nuclear plant reduced costs by 20% – or $10 million – annually.
Challenges of asset performance management (APM)
While asset performance management (APM) offers various benefits, organizations may encounter several challenges when implementing and maintaining APM strategies. Some of the key challenges include:
Data quality and integration
A major challenge in APM is ensuring data quality, consistency, and integration from diverse sources such as sensors, maintenance records, and enterprise systems. Poor data quality or lack of data integration can hinder the effectiveness of APM analytics and decision-making processes.
Complexity of asset ecosystems
Many organizations have complex asset ecosystems comprising diverse equipment, systems, and technologies. Managing and optimizing the performance of such complex asset ecosystems can be challenging, especially when assets are interconnected or operate in dynamic environments.
Predictive analytics and modeling
While predictive analytics and modeling are essential components of APM, developing accurate predictive models requires extensive historical data, domain expertise, and advanced analytics capabilities. Organizations may face challenges acquiring and analyzing relevant data, building reliable models, and validating predictions.
Change management and cultural shift
Implementing APM often requires organizational change, including shifts in maintenance practices, workflow processes, and corporate culture. Resistance to change, lack of stakeholder buy-in, and inadequate training can hinder APM adoption and effectiveness.
Final thoughts
Asset performance management (APM) is a comprehensive approach to managing the performance and reliability of physical assets throughout their lifecycle. APM reshapes operational dynamics by transforming how organizations manage, maintain, and optimize their physical assets. It enables organizations to move from reactive or scheduled maintenance to more proactive and predictive maintenance, resulting in increased asset reliability, reduced downtime, and improved operational efficiency.
The concept of reshaping operational dynamics through APM is closely connected to broader trends in digital transformation, Industry 4.0, and the Internet of Things (IoT). As the field develops, on-premise deployments could decrease. According to a report from Arms Reliability, vendors are offering cloud-based APM solutions, with APM-as-a-service available.
Overall, APM leverages advanced technologies and data-driven insights to drive operational excellence, enhance competitiveness, and deliver superior customer value. Ultimately, It helps organizations unlock the full potential of their assets and drive sustainable business success.