Manufacturing powers the world. From the car you drive to the device you’re reading this on, it all starts in the factory.
However, navigating from A to B isn’t straightforward. Manufacturers face pressure to innovate as they face changing market demands, technology, and the global economy.
Take COVID-19, for instance. At one point in the pandemic, US industrial production had its biggest monthly decline since World War II.
Despite these challenges, the demand for manufacturing remains strong. According to Deloitte, as of July 2023, annual construction spending in manufacturing reached $201 billion, a 70% increase from the previous year.
Manufacturing leaders must manage change well to stay ahead in a tough industry. Studies show that organizations that integrate change management are 47% more likely to meet their goals compared to 30% that don’t. However, only 34% of change initiatives succeed.
To ensure that change efforts work, leaders must grasp the basics, make a full plan, and recognize the importance of change management in manufacturing.
What is change management in manufacturing?
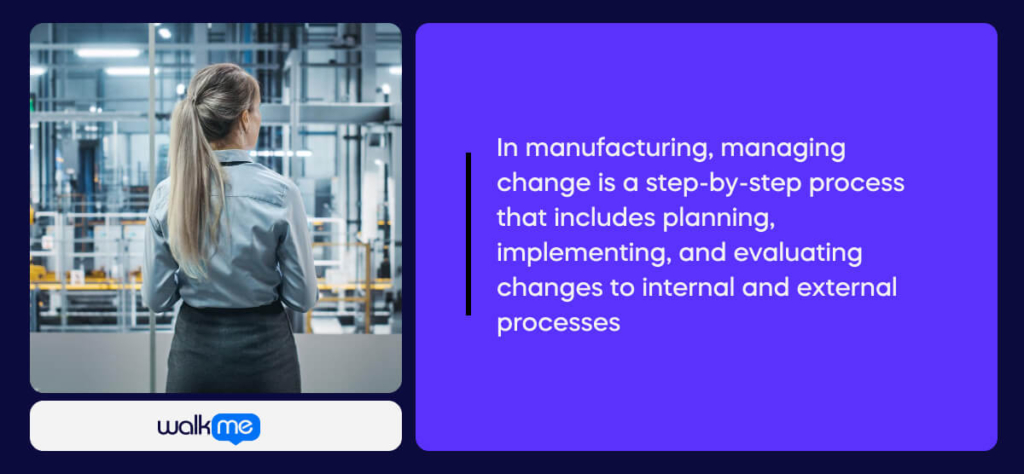
In manufacturing, managing change is a step-by-step process that includes planning, implementing, and evaluating changes to internal and external processes.
It’s a fundamental business practice that enables manufacturers to maintain productivity and profitability amid significant organizational or industry changes.
Why is change management in manufacturing important?
Manufacturing differs slightly from other asset-light industries. It involves managing production constraints within physical infrastructure and demands careful attention to people management.
Whether it’s producing and assembling materials, managing logistics and shipping, or ensuring responsible disposal or recycling of materials, manufacturing entails juggling multiple responsibilities simultaneously.
It’s an industry that is constantly evolving, and effective change management is crucial.
What are the types of change in manufacturing?
There are many types of change in manufacturing that industry leaders may address. Below is a list of the most common:
- Process changes: Implementing new methods or optimizing existing processes to improve efficiency and quality.
- Technology changes: Integrating new technologies such as automation, robotics, or data analytics to enhance production capabilities.
- Product changes: Developing or modifying new products to meet market demands or technological advancements.
- Organizational changes: Restructuring roles, responsibilities, or hierarchies within the company to improve communication, collaboration, and efficiency.
- Supply chain changes: Optimizing logistics, procurement strategies, and supplier relationships to ensure timely delivery and cost-efficiency.
- Regulatory changes: Adapting to new laws, regulations, or standards affecting manufacturing operations, safety, and environmental practices.
Best practices for managing change in manufacturing

Knowing the types of changes in construction is helpful, but it’s also key to understanding how to make changes well. Below are some of the best practices for managing change in manufacturing.
Cultivate relationships across the manufacturing change process
Manufacturing is not a one-team job. It hinges on effective communication between engineering and manufacturing. Fulfilling strong relationships between different departments is crucial to ensure successful change implementation.
A successful change initiative should involve all stakeholders in decision-making and have regular feedback sessions to identify areas for improvement. This approach enhances company morale and productivity and reduces the risk of employee disengagement across all levels.
This strategy is backed by countless research papers too. One recent paper by academics at Florida State University suggests that “stakeholder involvement, encouragement, organizational culture, vision, and mission” should be key when implementing organizational change.
Keep manufacturing change cycles short
A manufacturing cycle refers to the production process. It starts at production and ends at a finished product.
Focusing on fast production, short delays, and quick turnaround from raw materials to finished goods can greatly help.
Short change cycles allow manufacturers to quickly adapt to customer requests. They can also adapt to market trends and evolving needs. They do this with shorter change cycles. This flexibility is crucial in today’s fast-paced manufacturing environment.
Short cycles also reduce the risks of large inventory holdings and market fluctuations. This simplifies change implementation and mitigates potential challenges later in the process.
Use new technologies and real-time production data
Utilizing new tools such as technology and real-time production data for optimal results is also beneficial.
Real-time production data enables manufacturers to monitor and optimize their processes, enhancing efficiency and productivity. This data can identify bottlenecks, minimize downtime, and streamline workflows.
Leveraging technology and data can also reduce waste, inefficiencies, and maintenance costs.
Plan for risk mitigation
Planning for risk mitigation is another key component of effective change management in manufacturing. The world is unpredictable and the manufacturing industry is particularly vulnerable to external market conditions.
Take the COVID-19 pandemic, for instance, where disruptions to manufacturing caused widespread shortages across a wide range of products. To implement change effectively, leaders must account for potential risks, including stock shortages, changes in demand, and workforce challenges.
A well-prepared risk management plan enhances the organization’s adaptability, allowing for quick and effective responses to challenges as they arise.
This approach facilitates the smoother implementation of changes in manufacturing processes and boosts confidence among stakeholders, including employees, customers, and investors.
Five steps for managing change in manufacturing
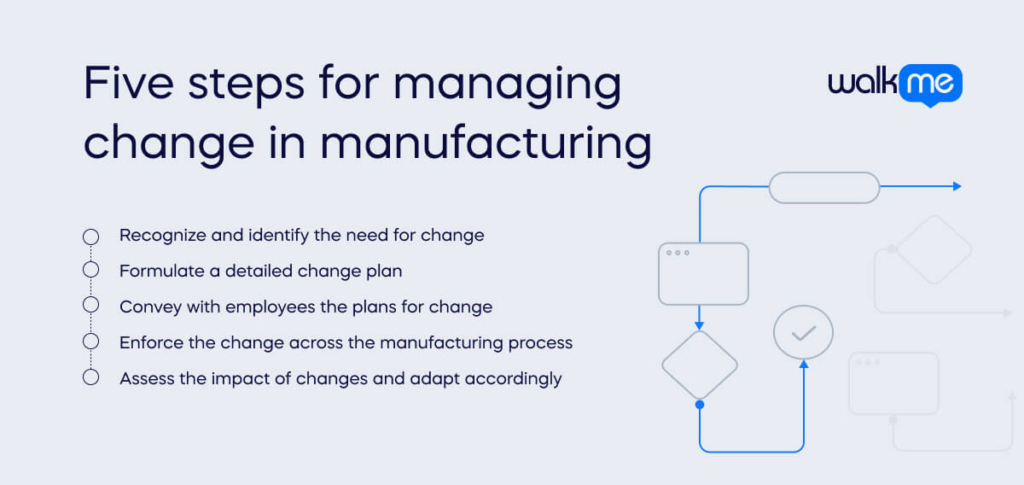
Change management is never easy. However, following these simple steps will increase your chances of success:
- Recognize and identify the need for change
The first and most important step in managing change in manufacturing is recognizing the need for it. Identifying specific areas where change would be beneficial is crucial in today’s rapidly evolving manufacturing industry.
According to a recent Deloitte report, 86% of manufacturing executives believe smart factory solutions are critical for maintaining competitiveness. Similarly, another report found that 76% of manufacturers adopt digital tools to gain enhanced transparency in their supply chains.
The change may involve physical upgrades or digital advancements. But, managers of change in manufacturing need to take a full approach to their operations. To effectively identify change needs, companies should conduct regular market analyses, monitor industry trends, and solicit feedback from employees and customers.
This proactive approach enables manufacturers to stay ahead of the curve and implement necessary changes before they become urgent.
- Formulate a detailed change plan
Formulating an action plan becomes equally crucial once the need for change is identified. This roadmap is the foundation for implementing change, ensuring change leaders have the necessary resources, and keeping operations on track throughout the process.
Developing a change management plan may seem straightforward, but requires careful consideration. The plan should be detailed, with specific dates and timelines to track progress. It should also outline clear objectives, resource allocation, and risk mitigation strategies.
Involving key stakeholders in the planning process is essential to secure buy-in and incorporate diverse perspectives.
- Convey with employees the plans for change
Another critical aspect of change management in manufacturing is effective communication. It’s crucial to convey the need for change to employees and stakeholders throughout every stage of the process.
According to Forbes, communication in change management should “include the reasoning for change and the expected impact.” The method of communication is also important. While mass emails may be effective for larger, hierarchical organizations, prioritizing in-person communication can help address resistance to change more effectively.
- Enforce the change across the manufacturing process
Once the change plan has been communicated, it’s equally important to implement the change across the manufacturing process.
Implementing change necessitates a systematic approach and ongoing effort. Every member of the workforce should understand their roles within the change process and the timeline for implementation.
Referring to the detailed change plan and monitoring all aspects of the workforce enables change leaders to identify strengths and weaknesses within the process and make adjustments accordingly.
- Assess the impact of changes and adapt accordingly
But it’s not just about implementing the change. Ensuring smooth change management is equally crucial. Continuous evaluation and adaptation are essential for long-term success in managing change in manufacturing.
Methods for assessing change effectiveness vary depending on its nature. However, effective communication across the workforce is critical for all change projects.
Regular feedback sessions, coaching, and one-on-one support are common strategies employed in manufacturing change management. These approaches enable manufacturers to pinpoint areas for improvement and make necessary adjustments.
What are the benefits of managing change in manufacturing?
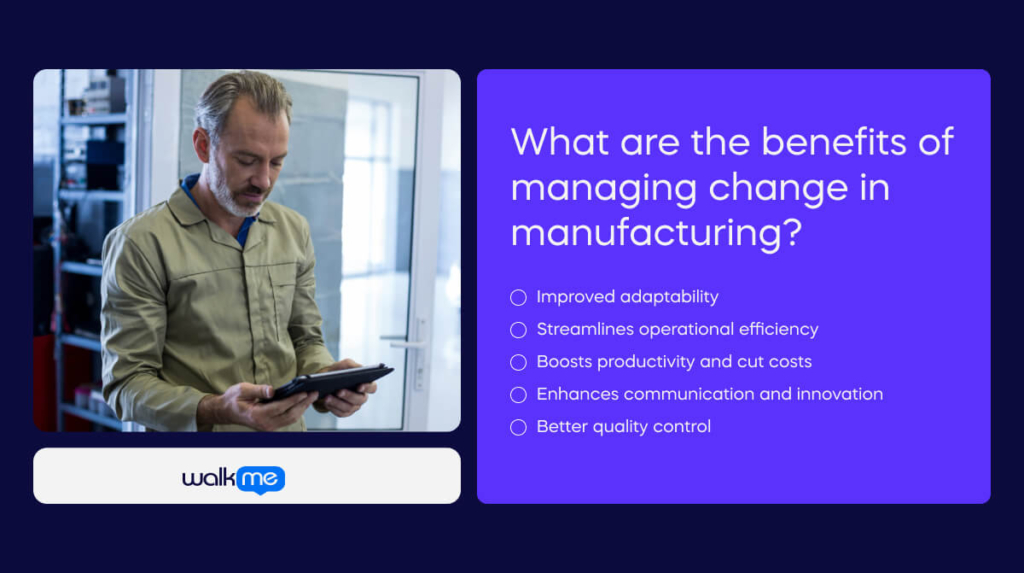
Despite the challenges, effective change management has countless benefits. Below are a few of the key benefits:
Improved adaptability
Effective change management enables manufacturers to adapt quickly to market conditions. The future is unpredictable, but adjusting to unexpected challenges is crucial for a manufacturing business.
Change management practices help manufacturers develop systematic approaches to adjust their processes, technologies, and strategies in response to evolving market demands, new regulations, or economic fluctuations.
Whether adapting company processes, integrating new technology, or refining strategies, this preparedness minimizes the negative impacts of unforeseen events such as supply chain disruptions or sudden shifts in customer preferences, allowing for quicker recovery.
Streamlines operational efficiency
Another key benefit of managing change in manufacturing is that it streamlines efficiency across operations.
The success of manufacturing hinges on effective communication across a wide range of teams, including engineering, product management, and supply chain management.
Managing change provides a structured framework for implementing new processes and strategies across the manufacturing business. Integrating new technologies into this framework, such as artificial intelligence, mobile apps, and robotic process automation, can be particularly effective in boosting efficiency.
Boosts productivity and cut costs
Managing change effectively can also boost productivity and cut costs.
Manufacturing relies on workforce productivity to keep the business running smoothly. Successfully implemented change management strategies can reduce the likelihood of employee burnout and increase engagement. This leads to higher morale across teams, greater trust in management, and overall boosts in productivity.
Effective change management can also lead to more agile business operations. This agility is beneficial for adapting to market conditions and unforeseen events like geopolitical tensions or pandemics. It can also lead to better resource allocation, reducing unnecessary expenses and minimizing costly defects and rework.
Enhances communication and innovation
Managing change can also increase workforce communication, collaboration, and innovation. When change is implemented correctly and when all members of the workforce feel valued, it can create a culture of openness and continuous improvement.
For this reason, the culture of a manufacturing company should be a key component of a change management strategy. Creating an environment where employees at all levels are encouraged to share ideas and feedback can lead to better problem-solving and the identification of innovative solutions.
Better quality control
Effective change management can also lead to better quality control, enhance a brand’s reliability, and reduce the risk of costly defects and legal fees.
When change is effectively managed, it often involves implementing new technologies, processes, and methodologies that directly impact product quality. For instance, adopting advanced quality management systems and data analytics tools can result in more precise monitoring and control of production processes.
But it’s not just about the product. Managing change can also benefit the workforce. Change initiatives usually include comprehensive training programs, ensuring employees are well-equipped to maintain high-quality standards.
Implementing new technologies, like mobile apps and messaging services, can also improve team communication, allowing defects and issues within the supply chain to be identified and communicated quickly.
What are the challenges of managing change in manufacturing?
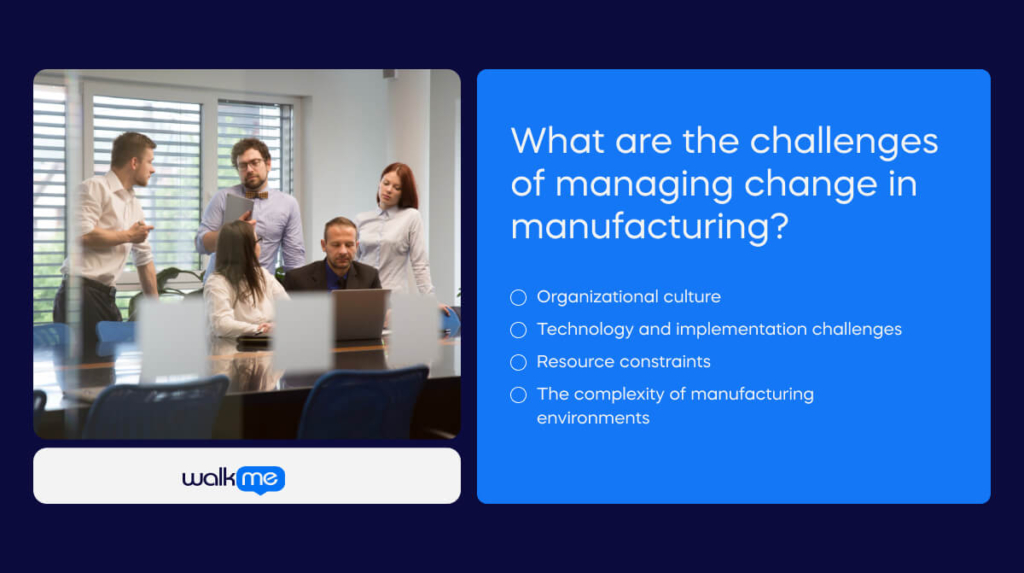
Here are some of the main challenges that those managing change in manufacturing should be aware of:
Organizational culture
The organizational culture of a manufacturing business can be challenging when managing change. Manufacturing companies are often hierarchical, giving employees rigid roles and duties.
This structure can be beneficial, allowing for efficient communication and management across a large organization. However, it can also lead to disengagement and resistance to change in the workforce.
This issue is prevalent across all industries, not just manufacturing. A Gartner study found that 44% of HR leaders reported their employees suffering from “change fatigue” in 2022.
Findings like this underscore the need for strategic communication to prevent burnout during change initiatives.
As a rule of thumb, ensure the workforce feels valued throughout the change project. This can be achieved through one-on-one feedback sessions, surveys, and group meetings.
Technology and implementation challenges
Leveraging new technology is another important aspect of change management in manufacturing.
As the industry shifts from human-powered manufacturing to data-driven solutions, change leaders must be aware of the associated challenges. Lack of training and improper implementation of these new tools can severely impact a change initiative.
To minimize these issues, ensure the workforce is properly trained on new technologies. For instance, if the change process involves a new supply chain management tool, all employees must understand its purpose and know how to use it effectively.
Online training workshops and coaching sessions are among the many ways to ensure that the workforce can use digital tools.
Resource constraints
Resource constraints are another key challenge in managing change in manufacturing. Due to economic shifts and changing market conditions, manufacturing projects often face tight resource constraints.
Limited resources can lead to mistakes, oversights, and reduced flexibility in responding to project challenges.
Manpower constraints, in particular, can affect team performance and morale.
Overburdening team members due to limited manpower or skill gaps can lead to burnout and decreased productivity.
The complexity of manufacturing environments
Another key challenge is the complexity of manufacturing environments.
Successful manufacturing requires precise coordination between various departments, such as production, supply chain, logistics, and maintenance. Managing change across this complex environment demands diligent planning.
Leaders should plan ahead to avoid issues that can arise from managing change in such settings. While the future is unpredictable, forecasting is essential.
It’s also wise to focus on adopting communication strategies across the entire workforce and integrate data-driven solutions and digital tools to facilitate communication in complex environments.
Streamlining the supply chain: Why managing change in manufacturing is crucial
Manufacturing remains a strong and profitable industry. However, despite its importance, the sector is vulnerable to changing market conditions, geopolitical tensions, and more. To ensure success, leaders must be adaptable.
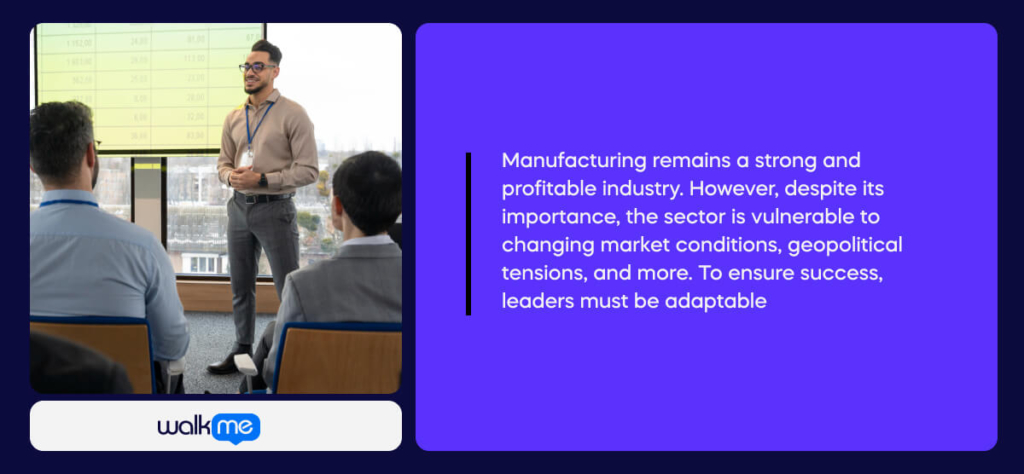
Change management is not easy, but diligent preparation can increase the chances of success. Leaders must involve all stakeholders in the change initiative to decrease the risk of burnout and employee disengagement.
They should also be aware of potential risks, plan for them appropriately, and utilize data-driven digital tools to maintain a holistic view of their operations throughout the change process.
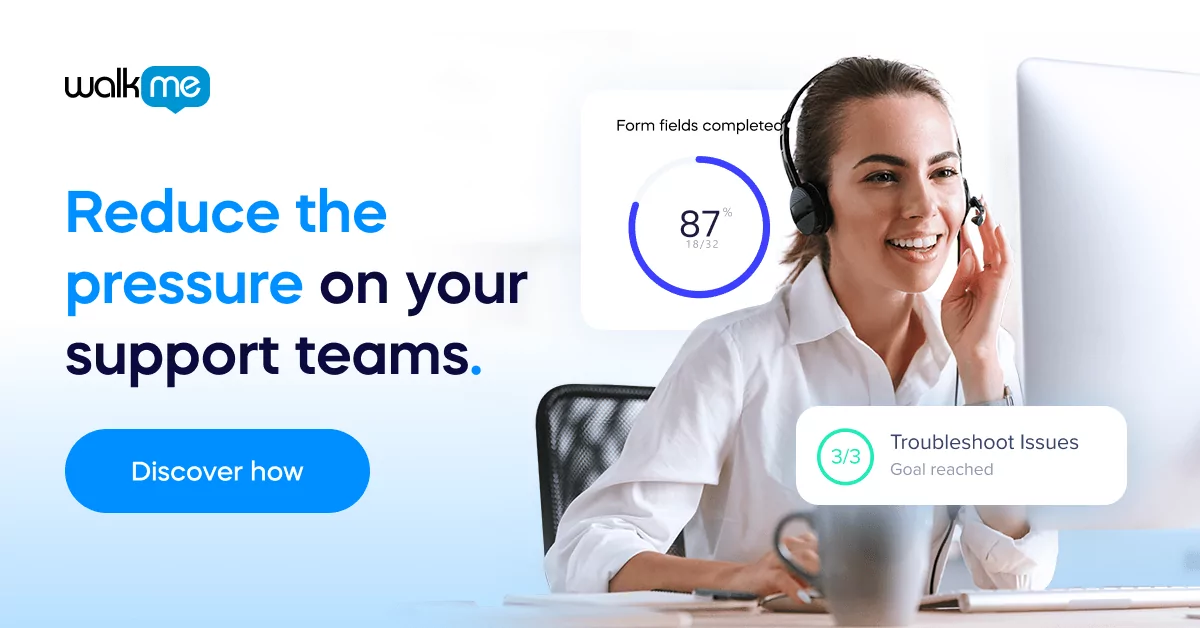