Businesses must evolve to remain viable, yet many need more internal resources or expertise to undertake a comprehensive and targeted approach to change. This deficiency often results in their process change initiatives being founded on shaky ground.
A significant obstacle for senior leaders aspiring to implement business improvements is adequate time to plan a change program that encompasses everything from the initial concept to the detailed specifics of process requirements.
Process change, or business process optimization, involves companies scrutinizing their current operational methods and implementing gradual modifications to enhance speed, efficiency, and dependability.
While many decision-makers concentrate on the intended outcomes and delivery methods, they frequently overlook the more profound examination of the procedures and operational practices that facilitate the change process.
When executed diligently, process change can yield sustained benefits for the organization and its employees, ensuring long-term success and adaptability.
This article will explore process change and its purpose, the types of existing business processes that can benefit from it, how to implement it within your organization, and provide practical examples of successful implementations.
What is process change?
Process change refers to the systematic approach of evaluating, refining, and enhancing existing business processes to boost performance, align with best practice standards, or elevate the quality and experience for customers and end-users.
This concept is known by various terminologies, including business process management (BPM), business process improvement (BPI), business process re-engineering, and continual improvement process (CIP).
Despite these varied labels, the core objective remains consistent: to diminish errors, reduce waste, augment productivity, and optimize operational efficiency.
What is the purpose of process change?
Every business operates on a foundation of various business processes, ranging from employee onboarding and financial transactions to IT issue resolution. These processes are integral to every aspect of business operations.
However, these processes are inefficient, taking longer than expected, consuming more resources than allocated, or yielding inconsistent outcomes. This indicates a breakdown in these processes, adversely affecting overall business efficiency. The extent of process change can vary greatly.
One approach is to comprehensively analyze the entire business, examining how tasks are executed at every level and pinpointing areas for potential enhancement. Alternatively, the focus could be narrowed to specific domains like customer care or resource management.
The underlying aim of process improvement, irrespective of its scale or focus, should always be to make the business run more efficiently, surpassing its previous performance.
What types of processes can benefit from process change?
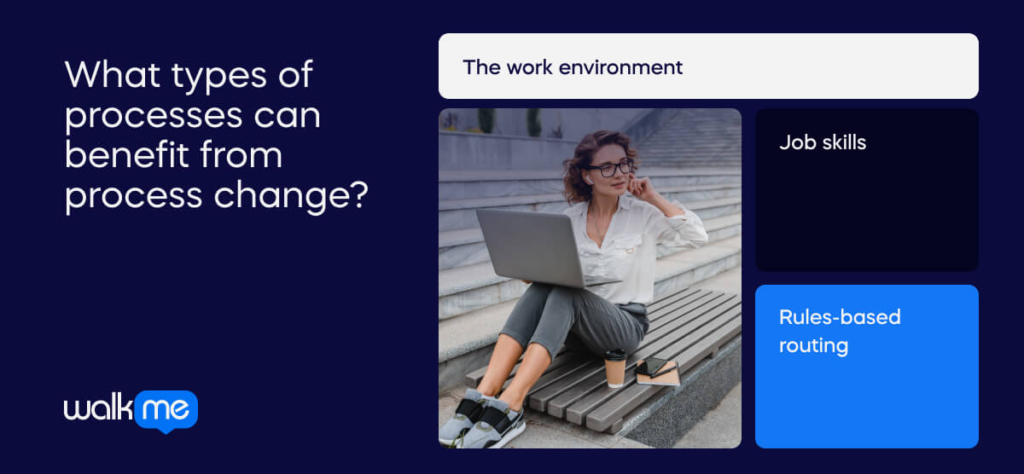
Enhancing efficiency in various business processes can significantly benefit them, thanks to process management methodologies like Six Sigma, the PDCA Cycle, Kaizen, DMAC, or the Theory of Constraints (enhancing efficiency in various business processes can significantly benefit them).
Take customer service processes, for instance. Automation in these areas can transform how customer inquiries are managed by digitizing and streamlining responses, thus reducing wait times for phone or email replies.
Business process automation simplifies tasks, enriches the customer experience, and increases precision by minimizing human errors. Automated systems can meticulously track orders at every production stage, promptly notifying staff of anomalies, mistakes, or delays in order fulfillment.
This approach helps organizations reduce redundancies, bolster process efficiency, and enhance the quality of their offerings.
Process change is also valuable in refining collaboration and communication practices. Effective cross-functional collaboration enables quicker identification of potential improvement areas than isolated departmental efforts. The importance of robust communication and collaboration is even more evident in the remote working era.
Technological integration facilitates process change, especially in automating traditionally paper-based tasks like vendor onboarding or complex request-for-quote processes.
Adopting digital methods for tasks such as rules-based routing and digital signatures streamlines operations and reduces the need for physical document handling. This shift makes document management more efficient and speeds up task and project completion.
Establishing a central management system for inventory, order tracking, and document organization is crucial for businesses like restaurants.
Using a mobile application for real-time inventory management and order placement enhances operational clarity and efficiency. Centralizing supplier information and protocols further streamlines the ordering process.
Improving the employee onboarding process is another area where companies can make significant strides. Implementing business process standardization that covers essential tasks like paperwork completion, policy comprehension, and technology system familiarization ensures new hires are productive from day one.
Such a system improves processes by reducing data entry errors and expediting onboarding, contributing to overall organizational efficiency.
How to implement process change

Initiating business process change can initially seem daunting. Questions like where to start and what to prioritize often arise. Modifying your processes isn’t a one-size-fits-all approach; it largely depends on making appropriate choices.
The following steps offer a solid starting point for developing your strategy for process change:
Focus on a specific problem that is not in line with business objectives
In process change, targeting specific issues rather than generic improvements is crucial. This approach ensures that efforts are concentrated on resolving urgent challenges, thus avoiding the unnecessary allocation of resources to already efficient processes.
A key aspect of process change is revisiting the company’s organizational goals. It’s essential to analyze how current workflows deviate from these objectives. This alignment helps pinpoint where changes are most needed and ensures that process improvements are goal-oriented.
Effective process change involves recognizing significant issues, such as an overly complex process in areas meant to be streamlined.
Identifying specific tasks or workflows that contribute to these overarching problems is critical. This helps in focusing improvement efforts where they are most needed.
Find the inefficiencies in the process associated with that problem
Once you’ve defined the problem clearly, you need to gather relevant data on the current process. This approach involves investigating the underlying causes of issues and developing targeted solutions to address them, ensuring that changes tackle the core of the problem.
Mapping out each step of the current process associated with this problem is vital to process change. This includes detailing every stage, calculating each step’s time, and identifying key personnel.
Understanding the flow of work and transition points between stages is essential for effective process improvement.
Using data and analytics is crucial in quantifying process inefficiencies. Process dashboards and other analytical tools can provide insights into areas that need improvement, allowing for data-driven decision-making in the process change journey.
Encourage stakeholder engagement in process change
Encouraging creativity and participation from all stakeholders, especially those directly affected by the processes, is vital. This collaborative approach generates innovative solutions and ensures buy-in from those involved.
It’s important to look for redundancies to eliminate and support frameworks to add, ensuring comprehensive improvement.
Detailing the required resources and tools for implementing change is also critical. Preparing a comprehensive business case helps garner support and buy-in from stakeholders, setting the stage for successful implementation.
Communicate the changes before roll-out
Once a plan to revamp a process is made, leadership must ensure clear and consistent communication about the changes to all stakeholders, including employee training for those involved in implementation. This assures everyone is on the same page and understands the new processes.
Test before all changes are made
Before full-scale implementation, testing the new process in real-world scenarios is advisable. This allows the relevant change team to make adjustments based on feedback and performance.
An iterative approach, gradually introducing improvements and continuously monitoring their effectiveness, ensures the process remains relevant and practical even as external factors change.
Ensure ongoing evaluation and adaptation
Once the new process is implemented, regular checks and evaluations are necessary to gauge its effectiveness and identify areas for further improvement. Adapting processes to evolving business needs and market conditions is a continuous requirement for efficiency and effectiveness.
Documenting improvements and analyzing key metrics before and after these changes provides concrete evidence of their effectiveness. This type of documentation is crucial for understanding the impact of the improvements and guiding future process change initiatives.
Practical examples of process change
Having examined process change implementation in the previous section, the focus shifts to ensuring the success of these methods.
Two real-world case studies will illuminate how businesses have effectively applied such changes in practical settings.
Lego
Orlando Machado, LEGO’s Chief Data Officer, explains how the LEGO Group encompasses many processes, from product design to consumer engagement, all of which are intertwined with data generation and consumption.
LEGO views AI as a critical tool to enhance these processes, whether improving the efficiency of molding machines, enhancing customer engagement, or creating engaging online experiences to complement physical play.
For example, LEGO utilized human moderators for the LEGO Life app to ensure safe content uploads. However, they realized the potential of training an AI agent to pre-screen content, mainly when children inadvertently include their faces in their uploaded pictures.
This AI implementation reduces the workload for human moderators by handling the initial content screening and improves the user experience for children. Instant content rejection by AI prevents situations where children might dismantle their creations before a human moderator reviews and possibly rejects their submission on the LEGO Life app.
This approach seeks an optimal balance between efficiency, process improvement, and customer experience.
Machado believes that such technology applications lead to moments of realization, where people see AI not as a threat but as a responsible tool that can significantly benefit their primary consumers, the children. This aligns with LEGO’s goal of enhancing experiences while ensuring safety and efficiency.
Shell
Shell, a company that has long focused on process optimization, is undertaking a significant AI initiative in supply chain, operations, and maintenance.
This initiative involves reengineering their work processes to adapt to a more distributed, diverse, and decentralized energy system, necessitating optimizing end-to-end processes at a scalable level. Rapid global deployment of solutions has become essential, transforming Shell into an AI-powered technology company.
In areas like monitoring and inspection at various facilities, tasks historically performed in person are now increasingly assisted by AI. This shift allows low-value-adding inspection to be performed remotely using robots and drones. Some Shell facilities, too vast for manual inspection, are now utilizing these technologies to automate processes and reduce cycle times.
This technological shift enables inspectors and maintenance technicians to shift their focus towards higher-value activities, such as project prioritization or advanced on-site verification.
For instance, before adopting a predictive maintenance program powered by C3 AI, equipment parts were either replaced periodically or upon failure, leading to either premature replacement or unplanned downtime. The AI-based approach has enhanced efficiency, reduced maintenance costs, minimized production disruptions, and prevented unexpected downtime.
Despite initial resistance, particularly from inspectors accustomed to traditional methods, gradual acceptance has been achieved as AI-driven processes’ accuracy and time efficiency are demonstrated. Shell actively involves engineers in rethinking work processes with remote surveillance centers, fostering a culture of change from within.
This AI-enabled process reengineering at Shell is evolving into a standard operational method. While individual projects may take a year or two, the more the company leverages digital and AI technologies, the more opportunities it sees for further enhancements.
This continuous improvement is especially vital as Shell transitions towards becoming a net-zero emissions energy company.
The pros and cons of process change
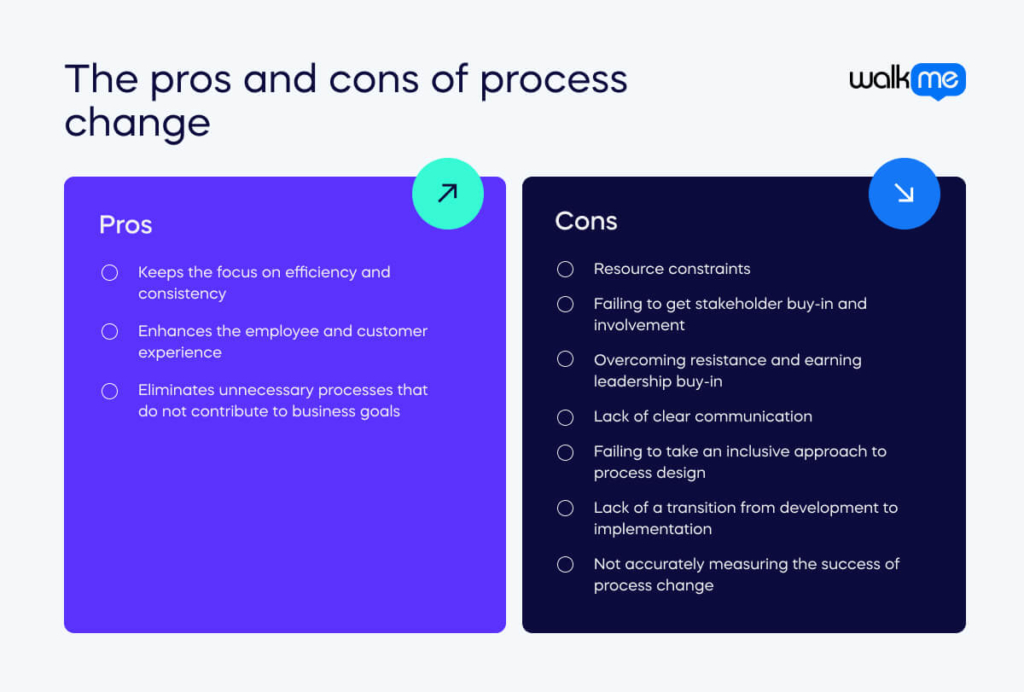
In a competitive business, a company’s distinctiveness often hinges on its operational methods.
Enhancing product and service quality and fostering employee satisfaction necessitates consistent evaluation and refinement of formal and informal processes. This practice aims to maximize efficiency in resources utilized (input) and results achieved (output).
Therefore, the primary advantages of implementing process change include:
Keeps the focus on efficiency and consistency
Implementing process change is essential as it helps teams focus on efficiency and consistency. Identifying areas for improvement enables an organization to adapt and grow in line with evolving market demands.
For example, a thorough review of business processes might reveal overlooked customer segments. Addressing such gaps can significantly enhance a business’s competitive edge.
A clear understanding and delineation of each stage in a process ensure that team members are aware of their roles and responsibilities, facilitating efficient information sharing and collaboration.
Another compelling reason to prioritize process change is the competitive landscape; if an organization isn’t continually refining its processes, it risks falling behind competitors who are.
Enhances the employee and customer experience
When processes are transparent and well-defined, employees are more likely to feel engaged and committed to their day-to-day work, resulting in greater job satisfaction and retention.
This positive internal environment translates into better customer experience, which can result in repeat business and overall company growth, making the investment in process improvement highly beneficial.
Eliminates unnecessary processes that do not contribute to business goals
One of the other key objectives of process change is eliminating unnecessary steps or procedures that use valuable time and resources.
Standardized processes align the efforts of all involved toward shared goals, reducing confusion, errors, and misunderstandings. This standardization is integral to ensuring smooth, error-free operations that support the business’s objectives.
But, in conjunction with its advantages, you must also consider the challenges of process change:
Resource constraints
Many companies need help with the limited availability of time, money, and expertise required for effective process change initiatives. Prioritizing resources and seeking external expertise can be vital in overcoming these constraints.
Failing to get stakeholder buy-in and involvement
The perception of process improvements being externally imposed without considering stakeholder views can lead to reluctance and resistance. Involving stakeholders in the change process fosters a sense of ownership and eases buy-in.
Overcoming resistance and earning leadership buy-in
Failing to contextualize changes or explain their purpose can lead to resistance among employees and leadership. Clear, transparent communication about the reasons behind changes is essential in overcoming resistance.
To deal with resistance, you could also try a change management model like Lewin’s Change Theory or the Bridges Transition Model.
Lack of clear communication
Neglecting to explain the rationale behind new processes can create confusion and even hostility. Recognizing that different groups have varying interpretations of process language is crucial for effective communication.
Failing to take an inclusive approach to process design
Designs influenced solely by a small group of stakeholders can be misaligned with broader business objectives. Including diverse stakeholders in the design phase ensures a more comprehensive and effective process change.
Lack of a transition from development to implementation
A disconnect between solution development and implementation can impede process improvement efforts. Ensuring stakeholders are comfortable and authorized to implement changes is crucial for success.
Not accurately measuring the success of process change
The success of process improvements is gauged by tangible outcomes such as time and cost savings or quality enhancements.
The effectiveness of process change depends on the actions taken post-implementation. Without practical application, the project may not achieve its intended goals.
Final steps on process change
Process change is a type of change that every organization must regularly engage in to stay competitive.
Relying on established methods may seem more manageable, but actively examining and improving workflows is crucial. This involves identifying weaknesses and experimenting with enhancements, eventually becoming a standard business practice. A critical aspect is to pinpoint and tackle the root causes of issues.
Misdiagnosing the problem or addressing merely its symptoms can lead to significant setbacks. Start by aligning with your overarching organizational goals, then determine where your current strategies are lacking. This approach ensures focus during the development of specific improvements.
Involving all relevant stakeholders is also vital. Their insights into existing processes and challenges not only provide valuable perspectives but also ensure their support when new improvements are introduced. People are more likely to commit to a business transformation they’ve helped create.
When implementing process change, it’s essential to record your company’s baseline metrics—customer churn, recurring revenue, or another critical indicator. After applying the changes, measure these metrics again. Remember, this type of change is iterative and agile, requiring continuous evaluation and adjustment.
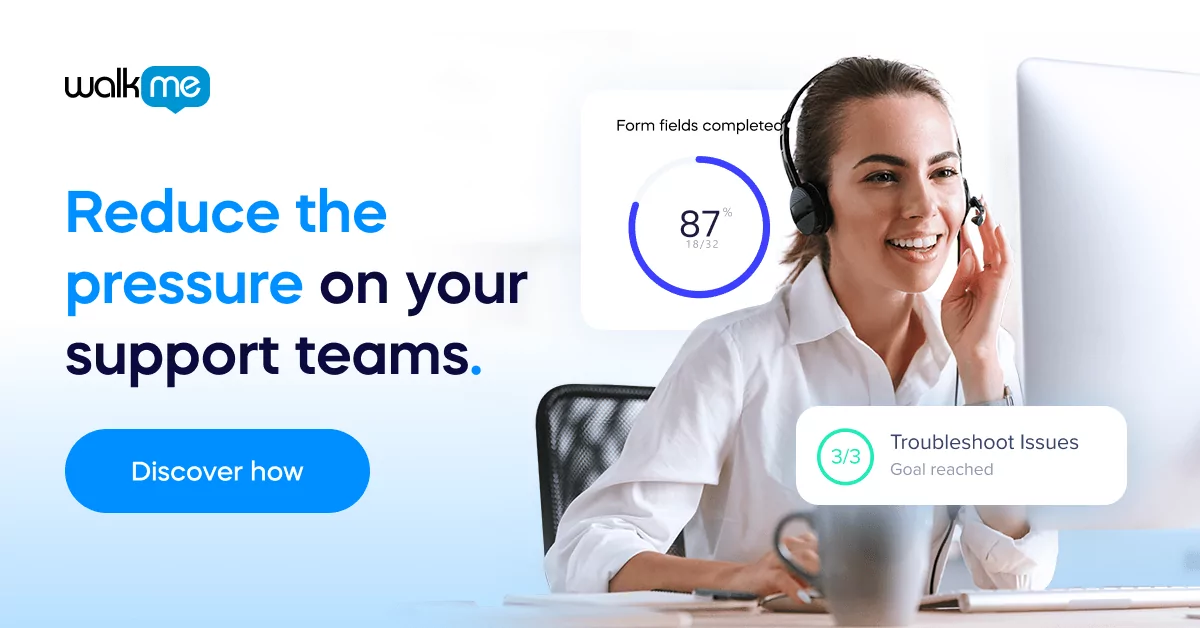