Process Mapping
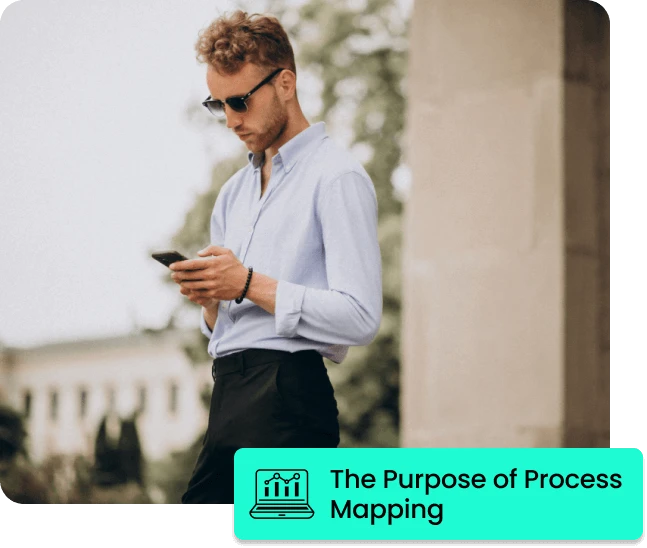
Table of contents
What is Process Mapping?
Imagine trying to learn how to perform a new job, but there are no clear steps to follow. It would be aimless, confusing, and inefficient. That’s precisely why process maps exist.
A process map is a visual of the flow of work. It’s a management and planning tool that guides users and employees through a series of events to produce specific outcomes. Other names for process maps include:
- Flowcharts
- Process flowcharts
- Process charts
- Functional process charts
- Functional flowcharts
- Process models
- Workflow diagrams
A process map details who and what is included in a particular process. It can be used in any business or organization. Process maps also let us see where and how a process could be improved.
Process maps use symbols to describe key process elements, such as:
- Actions
- Activity steps
- Decision points
- Functions
- Inputs/outputs
- People involved
- Time required
Each process element is indicated by a specific symbol, including:
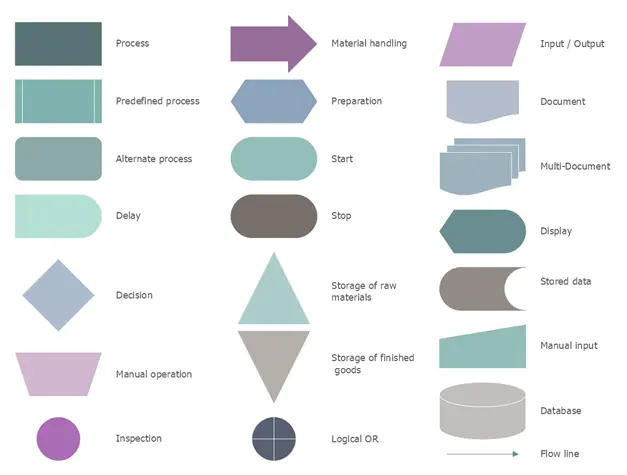
Image Source: cleverism.com
These symbols are part of the Unified Modelling Language (UML), which is the international standard for drawing process maps. There are almost 30 symbols that can be used, though the ones above are the most commonly used.
The Purpose of Process Mapping
As mentioned, process mapping serves to illustrate the steps involved in completing a certain action—or series of actions—to produce a particular outcome. It outlines who’s involved, and what they need to do. Process maps also provide insight as to how the process could be optimized.
Process mapping allows teams to brainstorm ideas, including ways to enhance the process itself. These maps support communication and provide process documentation. Mapping can aid especially in the identification of bottlenecks, delays, and redundancies. They further serve to define process boundaries, responsibilities, process ownership, and effectiveness measures.
Benefits of Process Mapping
Beyond the reasons for process mapping and its uses, there is much more to gain from mapping processes. They can pinpoint waste, streamline workflows, and increase understanding. They’re also more accessible and digestible than lengthy, technical written instructions.
Process maps and flowcharts can be utilized for:
- Planning projects
- Visualizing workflows
- Increasing understanding of the process
- Analyzing areas of improvement in the process
- Providing process documentation
- Improving communication about the process
Overall, process maps can save time and maximize efficiency by:
- Accelerating project design and creation
- Providing a clear embodiment of your ideas, information, and data
- Identifying problems and potential solutions
- Aiding in problem-solving and decision-making
- Simplifying complex processes into manageable steps
- Showing detailed connections and sequences
- Presenting an entire process from start to end
As well, process maps can help you better comprehend key characteristics of a given process, which can generate unforeseen solutions to issues your company or team may be facing.
Types of Process Mapping
Process maps are about communicating a process to others, allowing them to more fully understand the procedure.
There are a variety of types of process maps, and some of the more common ones are:
- Detailed Process Map – a highly detailed look at each step in the process.
- High-Level (SIPOC) Process Map – a high-level representation of a process that involves interactions between: Supplier, Input, Process, Output, & Customer (SIPOC)
- Rendered Process Map – illustrates current state and/or future state processes to show points for improvement
- Swimlane/Cross-Functional Map – breaks down sub-process responsibilities in the process.
- Value Stream Map – a technique management can utilize to improve processes required to make a product or provide a service to customers by finding what is valuable and what is irrelevant.
- Work Flow Diagram – a work process shown in “flow” format without the use of the UML symbols.
How to Create a Process Map
Creating a process map is a lot easier these days, thanks to software and low/no-code platforms, like digital adoption platforms (DAPs), that make it simple for everyone. DAPs offer code-free solutions that simplify and streamline employee and customer software activity. Some platforms include analytics that can be used to identify problematic steps in processes and AI can be leveraged to make optimal adjustments to those workflows.
Developing a process map is about communicating a process to others in order to achieve business management objectives. Here are some tips on how to create a process map that will enhance communication and understanding within your organization:
1. What’s the problem?
First, identify the problem you’re aiming to solve. What is the process that needs to be illustrated? The answer to this question will be the title of this map.
2. Brainstorm
Think about all the steps that would be involved—all of the activities that will need to be carried out. You don’t need to put the steps in order yet. The level of detail is up to you. Determine who will do what and when.
3. Set boundaries
Determine the boundaries for the process:
- Where or when does the process start?
- When or where does the process end?
4. What are the steps?
At this point, you can determine what the exact steps will be and put them in the proper sequence.
5. Flowchart symbols
Draw the basic flowchart symbols. Assign each process element its coordinating symbol.
(You can refer to the list of symbols presented earlier in the glossary entry by scrolling back up)
6. Finalize the map
This is the stage where you review the map with stakeholders and ensure everyone is in agreement. Be sure to include a title, date, and any other pertinent information.
Ask these questions:
- Is the process being run properly?
- Will team members follow the process?
- Does everyone agree with the process map flow?
- Are there any redundancies?
- Are there any steps missing?
Business Process Mapping
As we mentioned, process mapping can be used for any business or organization. A process in business consists of a group of interrelated tasks that happen as a result of an event. These tasks combined create a desired result for the customer.
Business process mapping can be used for:
- Business process improvement
- Business process redesign
- Re-engineering
- Operational output measurement
- Operational process design
- Documentation
- Process integration
- Mergers and acquisitions
Business process mapping is also useful for supporting compliance with manufacturing and service industry regulations.
Check out the entry “Business Process Standardization” for more information on the optimization of internal processes, or take a look at “Customer Journey Map” to learn about improving your externally-facing processes!